DaveG
Airbush Analyst
I got in the new Harder and Steenbeck Evolution 2024. I figure the best way to really get to know the brush is simply to use it the way it was meant to be used.
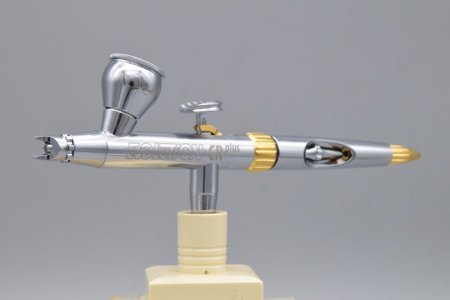
I did a google search, and decided on a Red-Eyed Tree Frog. I printed a full color 11"x14" reference photo, as well as a smaller (8.5"x11") print. I like to pre-mix many of the key colors that I will use in the illustration. To help with the process, I cut windows into a color image, mix my colors and paint full strength swatches. I place the swatches under the image, and check the color through the window - when you get them right, the window pretty much disappears. This is part of the technique(s) I learned from using Dru Blair's Classroom in a box "color theory". I will continue to build color and depth in the illustration itself. Having the majority of the base colors pre-mixed allows me to get into the meat of the work faster and more accurately (provided I did my job mixing).
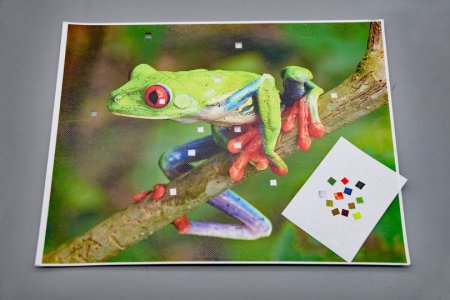
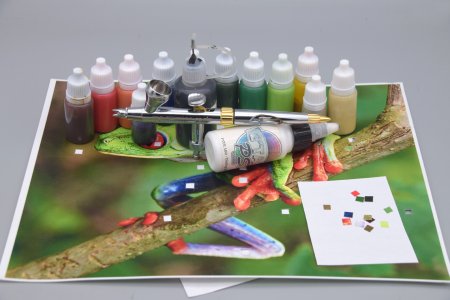
I will be working on a piece of fine weave canvas (11"x14") that I gave two light coats of gesso followed by a few good sealing coats of Createx UVLS clear. Still shows a good canvas texture while preparing the surface for some after application paint manipulation without damaging the weave of the fabric.
I'll add to the thread as I make progress...
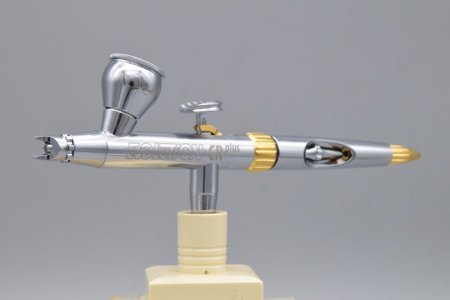
I did a google search, and decided on a Red-Eyed Tree Frog. I printed a full color 11"x14" reference photo, as well as a smaller (8.5"x11") print. I like to pre-mix many of the key colors that I will use in the illustration. To help with the process, I cut windows into a color image, mix my colors and paint full strength swatches. I place the swatches under the image, and check the color through the window - when you get them right, the window pretty much disappears. This is part of the technique(s) I learned from using Dru Blair's Classroom in a box "color theory". I will continue to build color and depth in the illustration itself. Having the majority of the base colors pre-mixed allows me to get into the meat of the work faster and more accurately (provided I did my job mixing).
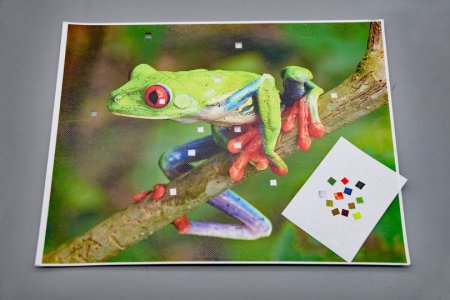
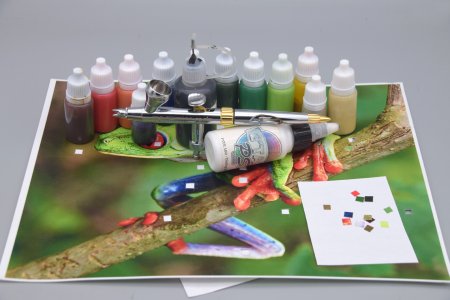
I will be working on a piece of fine weave canvas (11"x14") that I gave two light coats of gesso followed by a few good sealing coats of Createx UVLS clear. Still shows a good canvas texture while preparing the surface for some after application paint manipulation without damaging the weave of the fabric.
I'll add to the thread as I make progress...